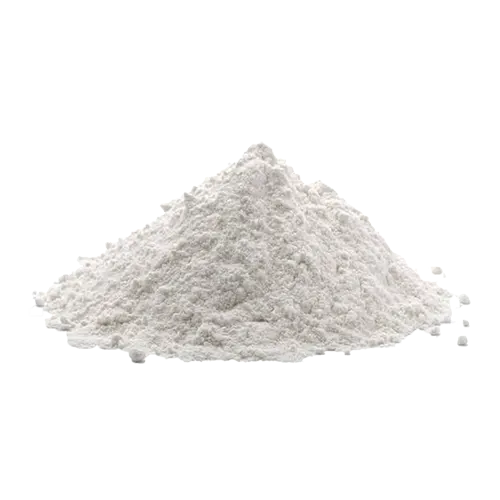
Green & Growth® Cellulose 100 % Hemp
Cellulose is the main building material of nature. It is the most abundant natural biopolymer on the planet, capable of replacing fossil-based materials on a massive scale.
GREEN & GROWTH®
Cellulose 100% HEMP
Green & Growth develops different types of cellulose, from lignocellulosic micro and nanofibers to more isolated forms such as nanocellulose, with different molecular characteristics.
Cellulose can be modified through various processes resulting in a wide range of applications.
Fibers 100% from industrial hemp, which guarantee a homogeneous behavior of the material, reproducible and open to any specific subsequent treatment of each final product. reproducible y abierto a cualquier tratamiento posterior específico de cada producto final.
Cellulose and by-products such as hemicellulose and lignin resulting from varieties of industrial hemp selected for their ideal proportion in molecular composition.
Green & Growth has designed different processes for different forms of cellulose. These processes are sustainable, mainly using organic solvents and organic acids.
Unlike the traditional pulping process, in which inorganic acids are used during the delignification and bleaching processes, Green & Growth has opted for a lignocellulosic starting fiber with a minimum lignin content that allows the use of respectful pretreatments.
Currently, the demand for lignocellulosic biomass is increasing for new applications in industries such as biocomposites, construction, and recently, cellulose has also attracted considerable interest as a source of raw material to produce nanocellulose.
The use of new sources of cellulose other than forestry, such as lignocellulosic fibers from Green & Growth, is essential due to the inability of the forestry sector to meet growing demand.
Non-woody biomass is particularly attractive as a source of cellulose for nanocellulose production due to its lower lignin content. This greatly facilitates the purification of nanocellulose in terms of performance, purity, and the use of gentler and more environmentally friendly methods.
Industrial hemp stands out as a source of cellulose for:
- Its high cellulose percentage compared to wood sources and other herbaceous sources.
- Its low lignin content compared to wood sources (1-10% vs. 20-35%).
- Its high photosynthetic efficiency, which results in rapid growth with a biomass weight yield 5 times greater than forestry sources through our cultivation methods.
- The arrangement of cellulose microfibrils in the molecular structure of hemp tissues, which imparts special mechanical properties to derived products.
- Low use of additives for growth and production.
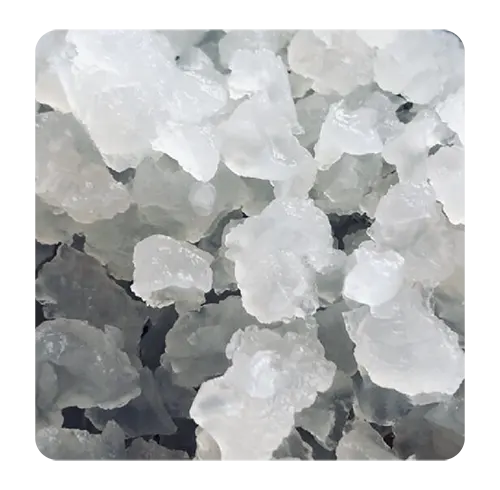
NANOCELLULOSE:
Material for the Future
Nanocellulose is the leading candidate for the technological revolution in materials, as it has the potential to improve the technical capabilities of cellulose fibers when incorporated into products such as biocomposites or other construction materials.
For example, in one of its isolated forms, nanocellulose exhibits unique properties:
- Mechanical properties, such as high strength and elasticity.
- Thermal properties, such as high thermal stability with a low coefficient of expansion.
- Rheological properties, such as a high storage modulus.
- Optical properties, such as high transparency.
- Physical properties, such as lightweight.
- Chemical properties, such as high specific surface area, high chemical reactivity, biodegradability, and biocompatibility.
APPLICATIONS
Nanocellulose has broad potential applications in the food industry, packaging, water purification, paper manufacturing, biomaterials, and more.
Although nanocellulose is still under research, there is expected to be significant growth in its global market due to its versatile applications and potential to replace not only less sustainable resources like graphene but also other resources that are expected to become limiting, such as lithium.
Therefore, nanocellulose is considered one of the most advanced and promising materials for the future, thanks to its remarkable technical and environmental properties.
Polymers reinforced with natural fibers have become one of the most popular methods for improving the mechanical characteristics and sustainability of polymers.
The incorporation of cellulose in its various forms, such as lignocellulosic fibers, cellulose microfibers, cellulose nanofibers, or crystalline nanocellulose, significantly enhances the mechanical properties of biocomposites.
Each bioreinforcing agent has particular properties, so the most suitable one should be evaluated depending on the process. In any case, it is widely accepted that the use of nanocellulose enhances the unique properties of natural fibers, such as low weight, high elastic modulus, dimensional stability, low thermal expansion coefficient, tensile strength, elongation at break, transparency, and impermeability.
Nanocellulose can be applied to various plastic matrices such as PP, PET, PLA, PVA, rubber, tires, or other materials such as natural rubber.
Nanocellulose has the potential to make electronics biodegradable. Currently, cellulose's applications in electronics are expanding into areas ranging from insulation to energy storage, screens, semiconductor devices, and even solar cells.
In recent years, green electronics based on cellulose biopolymers have been complemented by lightweight, portable, and flexible energy generators based on nanocellulose to provide power to portable electronics through the collection of mechanical energy in triboelectric and piezoelectric devices. The significant ecological advantage of electronics and thermoelectric devices based on nanocellulose is their inherent biodegradability. As these devices have become ubiquitous in modern society and prevail in all facets of human activities, and the lifespan of electronic devices is getting shorter, the pressure on electronic waste management systems is increasing. This poses a growing environmental problem, and an alternative to traditional electronics is biodegradable electronics as the most viable replacement to address the problem of uncontrolled electronic waste and reduce the environmental footprint of devices.
Recently, nanocellulose has been used to prepare porous carbon for use as a high-performance supercapacitor electrode.
Nanocellulose can be used in energy storage systems, paper batteries, supercapacitors, paper displays, biosensors, as well as in various electronic and optoelectronic devices. These include transparent transistors, light-emitting diodes, solar cells, antennas, radio frequency identification devices, high-performance speakers, and lightweight actuators.
It can also be used for the manufacture of smart materials capable of changing their shape, properties, or behavior in response to electrical inputs, light, temperature, pH, magnetic force, or other stimuli to develop sensory actuation systems.
Therefore, the technological possibilities of nanocellulose are immense and have the potential to lead the next technological revolution.
The use of nanocellulose during paper formation or even for the coating of formed dry paper, can improve the bond between cellulosic fibers by creating new hydrogen bonds between cellulose and nanocellulose fibers, enhancing strength, softness, printability, and overall physical-mechanical properties.
This positive effect on physical and mechanical properties also occurs when applying nanocellulose to the surface of cardboard, eliminating the need for synthetic reinforcement materials.
Using hemp lignocellulosic fibers would allow the production of cellulose pulp for paper or cardboard making, and nanocellulose fibers can be used for paper or cardboard coating. Hemp can completely replace wood-based cellulose sources to produce high-quality paper and cardboard.
Furthermore, the production and coating of paper or cardboard exclusively with hemp-derived cellulose would constitute an environmentally friendly production method, as it involves a non-forestry starting raw material with multiple environmental benefits and environmentally friendly delignification methods, unlike traditional paper production methods with inorganic acids and bleaching treatments.
Food packaging waste is a significant environmental and health problem affecting millions of people worldwide. Food packaging contributes to pollution, greenhouse gas emissions, resource depletion, and exposure to harmful chemicals.
Food packaging waste can also pose serious health risks to humans, especially when it contains chemicals that leach into food or the environment. Some of these chemicals, such as bisphenol A (BPA), phthalates, and perfluorinated compounds (PFCs), disrupt the endocrine system, affect reproductive health, and increase the risk of cancer and other diseases.
Even new attempts to generate disposable and sustainable food packaging and supplies have generated controversy due to the presence of perfluoroalkyl substances (PFAS), which are highly harmful to health and the environment, as waterproof coatings on all these new paper or cardboard products.
Nanocellulose possesses the necessary properties to become a coating that provides gas and water impermeability to all cardboard and paper for food packaging or for food disposable use. In addition, nanocellulose would be non-toxic, biodegradable, and renewable.
Barrier properties depend on the type of nanocellulose, film density, porous structure, and lignin content and distribution.
Crystalline nanocellulose has high crystallinity and purity, giving it improved biocompatibility for various biomedical applications. Biocompatibility is the ability of a foreign material to be implanted in the human body without causing reactions.
Thus, nanocellulose can be used in the production of biosensors for detecting proteins, enzymes, or metals in any aqueous medium, which is very interesting for both the medical field and water quality control.
Among other medical applications, is the use of nanocellulose to produce harmless and easily disintegrable coatings for human pills.
Nanocellulose has the ability to act as a radiation filter in all three ultraviolet zones: UVA, UVB, and UVC. This, combined with its biocompatibility and non-toxicity, makes it a promising material in the medical, cosmetic, and textile industries.